FOCUS #3 - A three-part dial, a play of textures on two levels
- Thibault
- Oct 9, 2024
- 3 min read
In watchmaking, each component plays a crucial role in the aesthetics, precision and durability of a watch. The dial, a true interface between mechanics and visuals, is distinguished not only by its design, but also by the technical choices that guide its design .
From material selection to production techniques, this article explores the manufacturing process and unique features of this three-part dial.

- MATERIALS & CONSTRUCTION
Machining
Brass was chosen to make this complex triple-decker construction. This non-magnetic material is known for its lightness and polishing properties. It also offers strong corrosion resistance when electroplated. Electroplating consists of depositing a thin protective layer of metal on the surface of the brass in order to improve its durability and resistance to external elements.
However, it is mainly for its malleability that this material was chosen for the construction of the series. Its unique properties allow it to be worked by stamping (die casting) and punching (perforation). These two techniques are essential for the manufacture of the different levels of dials in the series.
Three separate parts are machined separately and then reassembled at the end of the process. Using a snap-fit mechanism, eight punched holes secure the two upper dials to the lower holding base, forming a unified structure.
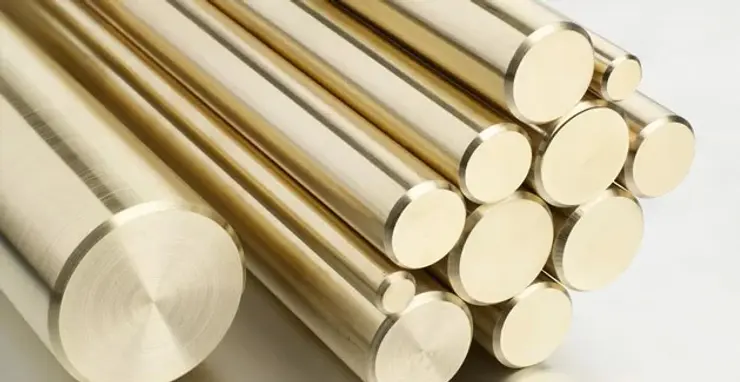

- THE HOLDING PLATE
Lower dial
A mold is created ex nihilo for machining the lower plate. The latter allows, by stamping (pressure of the mold on the brass), to give the desired shape to the part.
This technique thus offers the possibility of creating complex shapes and a uniform grain on the lower part. So that the minute graduation and the moon age also appear precisely, these are directly incorporated into the mold. This results in a blank finishing tray.
A punching is then carried out to create the eight holes allowing the assembly to the caliber and the fixing of the dial. These multiple holes will also allow the two upper stages to be fixed, nested and securely held on the plate.
Finally, square brackets are manually welded at 01H - 02H - 04H - 06H - 07H - 08H - 10H and 11H to support the semi-flying appliques.
Once the raw piece is finalized, the dial is electroplated to create a protective layer, before the color is applied. Then follows the white or black decal of the minute and lunar graduations.

- THE TWO FLOORS
Hour ring & moon window
From a blank, three openings are punched on the central dial: the moon phase window, the date window, and the central opening for the hands. This method creates a fine slope around the moon phase window to emphasize its contours, as well as an extra thickness around the date window, as a reminder of the lower dial.
The construction of the outer dial is simpler, with a ring cast to fit precisely to the lower dial . The same treatment is then applied as for the base plate: an initial finish to remove imperfections, electroplating for durability, and application of the background color. In addition, eight retaining flanges are drilled into the back to ensure optimum fixation.
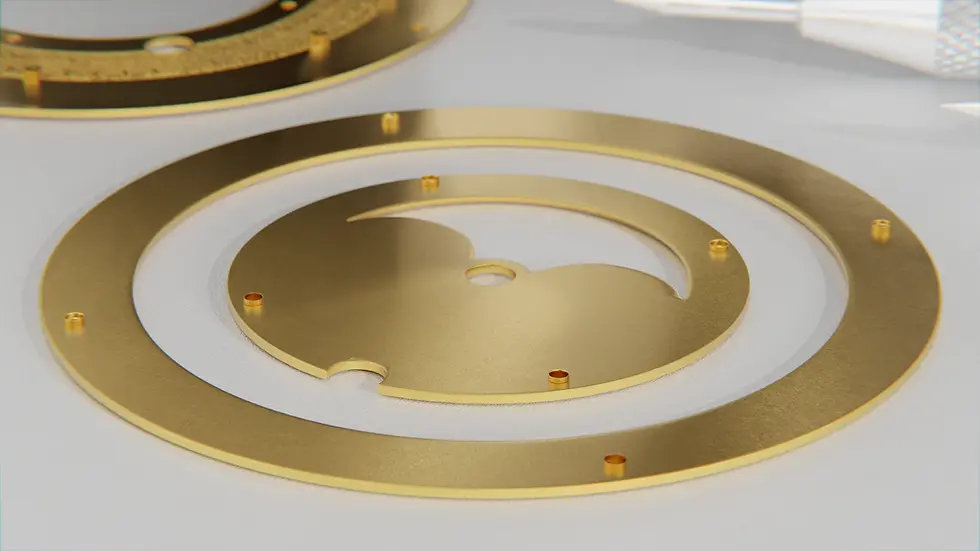
Several successive decals follow, in order to create a relief on the graduation . The three triangles in Luminova are also positioned by successive decal, in order to ensure precision in the application, from a mixture of paint and Japanese Luminova.
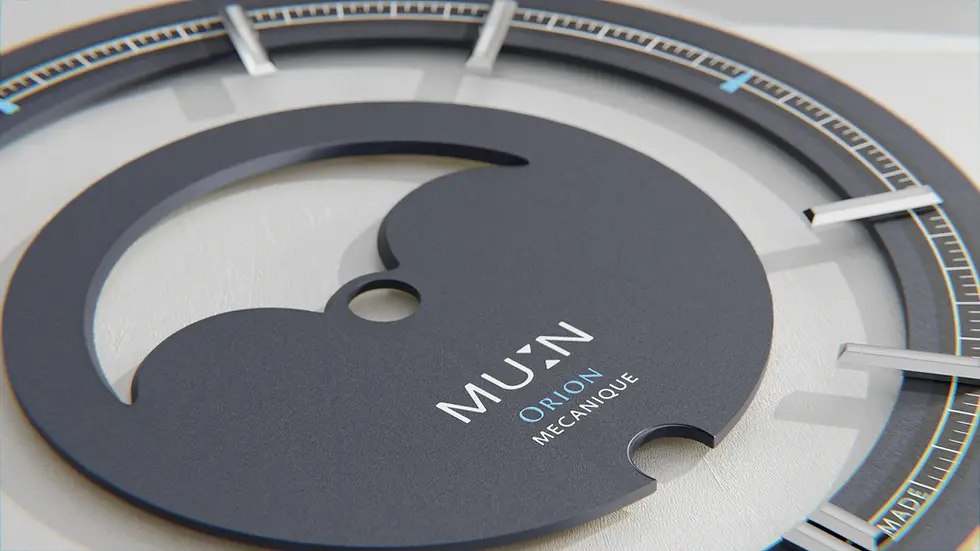
- ASSEMBLY OF PARTS
Creation of the dial
The three different levels are finally inspected individually before assembly. The latter are manually clipped at the level of the eight retaining flanges. Hollowed out in their center, a welding point allows an optimal attachment between the different parts.
The indexes are finally manually positioned with two fixing points: on the outer ring, and on the lower plate. The Luminova is also applied by hand in the hollow of each index.

- PROTOTYPING
Conclusion
The ORION series' three-part dial design is the result of a meticulous process, combining advanced machining and manual design.
Numerous versions of prototypes were thus created throughout its design, with work focused on durability (adding applique supports, welding the highlights, thickening the dial, etc.) and aesthetics (various tests on the contours of the windows, the matte or satin finishes, the size of the grains, or even the colors).
I hope this article has brought you new perspectives on the manufacture of the series dials. We will soon discuss the SW caliber in a next dedicated FOCUS.
Comments