The manufacture of a strap in 10 steps, from the choice of leather to the leatherwork
- Mu:n
- Apr 7, 2023
- 4 min read
Updated: Apr 12, 2023
On this Friday, April 7th, we finally have in our hands the series prototypes of the Artemis project. Manufactured by a historical actor in French leather goods, no less than fifty steps are necessary for each of their realizations.
In this article, we offer you the opportunity to learn more about these straps, their leather, and their manufacturing process.
What is calf milk leather ?
Calf milk leather leather is a type of leather coming from young calves. Finer and more flexible than adult cowhide, this choice provides the straps with a soft texture to the touch. By choosing this type of leather, we aimed to take into account your feedback on the importance of a flexible and pliable strap. We, therefore, opted for a naturally elastic and malleable leather.
With finer collagen fibers, calf milk leather is more durable, less susceptible to scratches and wear, and has exceptional resistance to environmental conditions and moisture. This durability allows for easier maintenance, as regular cleaning with a damp cloth is sufficient.
Finally, unlike adult cowhide leather, which sometimes has marks, scars, or imperfections, calf milk leather has a uniform and regular texture. Also, its natural shine provides a raw charm and aesthetics without retouching. Although more expensive, the origin of this leather comes 100% from small Franco-Italian cattle farmers, whose leather goods SIS ensures the supply. We are aware of the importance that enthusiasts attach to the quality of strap and we wanted, for this first collection, a leather that meets your requirements.

What is Alsavel and why use it as strap lining?
For the lining, we chose a material that is very popular in leather goods: Alsavel. A synthetic material, it has several advantages. First of all, it is lighter than genuine leather, which makes it comfortable to wear for long periods. It is also much more resistant to water and moisture and is easier to clean. Initially developed in France in the 1970s to replace genuine leather in shoe manufacturing, this synthetic material quickly spread to other industries, including the watchmaking industry.
Strap Manufacturing in 10 steps
Selecting the leather is only the first step in the process. The true accomplishment lies in the expertise required to manufacture the strap. Close to 50 steps are necessary to produce this precious piece that enhances our timepieces: cutting, skiving, dyeing, polishing... We had the opportunity to follow the manufacturing process, and we summarize it in 10 steps:
Leather cutting: The leather is cut to the required dimensions for the strap, usually 20-25 cm. For small-scale production, a special cutter or punch is used, but for Mu:n straps, we utilize a laser machine.
Marking the stitching points: The stitching points are marked on the leather using a pen or marking tool. The stitching points are typically evenly spaced on the strap for a uniform appearance.
Punching the stitching holes: The stitching holes are punched using a specialized punch tool. The holes are placed along the marking lines to ensure the stitching points are even and aligned.
Assembling the different layers of the strap: Mu:n straps are composed of several layers of leather, which are assembled and glued in place. Intermediate layers of synthetic materials are also added to reinforce the strap's strength and durability.
Sewing the edges: The two edges of the strap are then assembled and sewn together to form the strap. The sewing is done using a special sewing machine for leather. The sewing thread used is usually nylon or waxed cotton for increased strength.
Gluing the edges: After sewing, the strap edges are glued to reinforce the buckle area and prevent the leather from fraying. A strong, water-resistant adhesive is used to increase the strap's durability. This delicate step is done by hand by our partner SIS. Adhesives used for leather are typically latex-based, epoxy-based, or polyurethane-based, which have strong adhesion and good resistance to water and weather.
Adding the loops: The loops are added to the strap using a special sewing machine. The loops can be made of metal or leather and are sewn in place to secure the strap.
Attaching the buckle: The buckle is then attached to the strap using a special sewing machine. The buckle can be made of metal or leather and is sewn in place to secure the strap.
Applying the lining: If the strap has a lining, it is cut to the strtap's dimensions and glued in place using a special leather glue.
Finishing the strap: Once the strap is assembled and glued, the edges are smoothed to give a professional and pleasant touch. Layers of cream or wax can be applied to protect and maintain the leather over time.
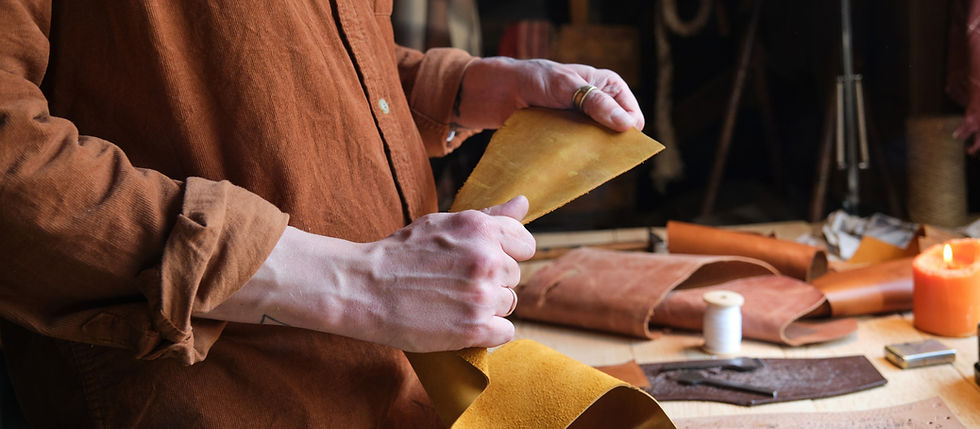
The SIS Group, the history of our leather goods partner
In 1983, Jean Pierre Tolo and Patrick Brenier created SARL Supercuir in Avoudrey in Franche-Comté, a company specialized in the manufacture of watch straps. For nearly twelve years, they equipped employees with sewing machines at their homes, who delivered the fruit of their labor to the company every week. Over the years, the company grew steadily and continuously.
In 1998, the company changed its name to SIS and focused on creating high-end leather goods to move into the world of luxury and fine watchmaking. SIS also launched the Ecole de Maroquinerie d'Avoudrey (EMA) in 2011, allowing it to train internally and integrate up to more than 100 new employees each year.
After 30 years of existence and experience, SIS has been able to maintain the values of a family and artisanal company while adapting to the latest technologies. With more than 1000 employees in France, the company has maintained a local base and French legitimacy, while committing itself to an ethical approach that respects the environment and its employees. Since March 2023, SIS has taken over the entire leather range of Mu:n Projects, following a collaboration initiated in January 2022.
You can find out more on the SIS Group website.

Comments